聚焦中核二三“四大使命”、“四大转型”和二十项重点工作,围绕焊接施工过程的“精益化、自动化、数字化”管理,中核设计焊接研究所工程数字化焊接研究中心(简称“研究中心”)积极践行“小核心、大协作”创新理念,构建“产、学、研、用”一体化布局;充分协调各方优势资源,在焊接数字化关键技术创新取得了重要进展。截止目前,研制完成的物联网焊机已累计应用1500套,用户涉及二三公司内部、集团公司内外部等17家单位.
研究中心立足于太平岭项目部焊接数字化需求,克服了技术难度大、需求细节多、研发周期短等困难,加班加点,历时4个月成功研发了基于传输数据高效的4G/5G通讯的焊接物联网系统。
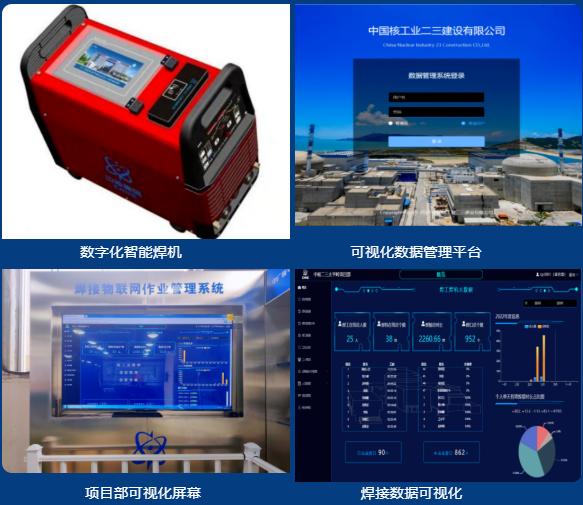
该系统于2022年7月开始在项目部车间及核岛内正式应用,首次实现了将核岛内约85%区域焊接施工数据实时传送至外部可视化界面,该系统具有焊接参数和有效工时实时采集、工艺电流智能控制等功能,对于促进公司项目精细化管理和数字化转型将发挥重要的作用。
2、优化集成电路,大幅降低焊接装备成本
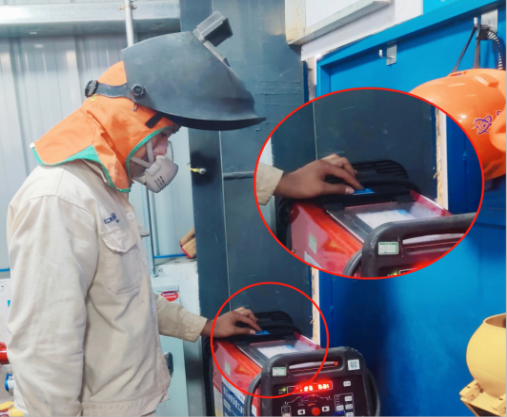
为降低焊接物联网系统成本、丰富焊机应用场景、增加焊接安全性,研究中心团队人员通过对焊机内部电路重新集成开发以及Lora/4G/WIFI等多种通讯方式研发,优化了焊机内部空间,增强了焊机的通用性、网络性和安全性,样机销售价格比原先焊机降低1/3以上,全面提升了焊接物联网系统市场竞争力。目前,新研发的数字焊机已在夹江项目开始试用。
3、AI+视觉传感,焊材发放回收系统
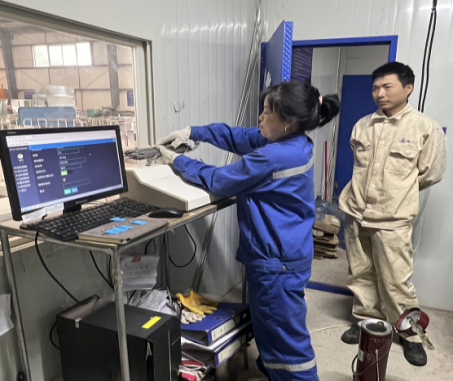
为解决目前现场焊材发放回收过程中消耗大量人力成本、发放回收记录不易统计等痛点问题,研究中心通过引入“AI+视觉识别系统”,历时近3年时间,经历了三次迭代升级,自主研发了焊材发放回收系统。期间累计采集各类焊条头样本50余万张,训练筛选20余种判别模型,模拟上万次实验,于2022年7月在公司夹江项目投入应用。该系统可高效、精准地完成焊材的发放回收,效率较人工提高2倍,可实时记录系统,实现无纸化管理,可采用焊工卡片进行身份识别,避免了焊工代领误领的情况。
面向未来,中核设计焊研所数字化焊接研究中心将进一步思考焊接数字化深化变革方向,构建焊接全流程全要素数字化系统,实现焊接数字化向数治化转变,更好地落实中核二三“四大使命”、“四大转型”及“数字化”要求,更好地服务于项目施工精益化管理,为公司创新发展创造更多的效益和价值。
免责声明:本网转载自合作媒体、机构或其他网站的信息,登载此文出于传递更多信息之目的,并不意味着赞同其观点或证实其内容的真实性。本网所有信息仅供参考,不做交易和服务的根据。本网内容如有侵权或其它问题请及时告之,本网将及时修改或删除。凡以任何方式登录本网站或直接、间接使用本网站资料者,视为自愿接受本网站声明的约束。