国家科技重大专项高温气冷堆核电站示范工程(以下简称“高温堆示范工程”)经过9年施工建设,于12月20日首次并网发电。这是我国先进核电技术自主创新取得新胜利的一步,也是我国核能领域坚持科技自立自强、推动落实“碳达峰、碳中和”目标实现和中国核工业高质量发展的重要成果。
高温堆示范工程从科研设计、施工建设,到球形核燃料元件和重要装备研制,最终成功并网发电。各相关领域有两三代核能人为此奉献了青春和智慧。《中国核能》自2021年第四期起隆重推出“见证——高温堆进行时”专题系列报道,讲述高温堆示范工程建设者们书写青春、挥洒汗水,全力以赴铸就国之重器的奋斗故事。让我们启航去见证这些非凡的成就!
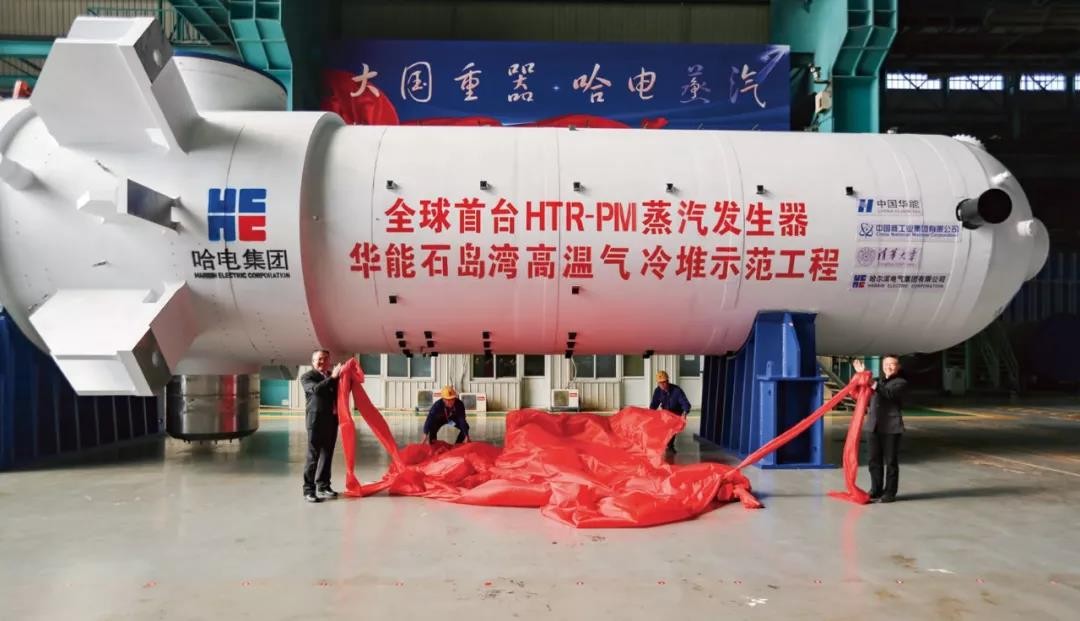
2018年10月31日,首台蒸汽发生器发运仪式
2021年12月20日,华能石岛湾高温气冷堆核电站示范工程成功实现首次并网发电,机组各项运行指标正常,反应堆、汽轮发电机及相关系统设备运行稳定,标志着我国核电科技创新取得重大突破,实现“换道超车”、全球“领跑”。成功并网的成绩背后,离不开运行可靠的关键设备。
高温堆示范工程核岛及BOP设备共计15000余台套,其中2200余台套属于工程首次使用,660余台套属于创新型设备。核岛设备采用EPC总承包模式,其中,核岛主设备如反应堆压力容器、蒸汽发生器、堆内构件、热气导管、控制棒驱动机构、主氦风机、DCS等为业主与总承包单位联合采购、平行监造;常规岛设备由业主自行采购、委托监造。项目建设过程中,中国华能组织清华大学、哈电重装、上海电气等关键设备研制团队日以继夜砥砺奋斗、联合攻关,攻克了多项“卡脖子”技术,攻克了蒸发器超长传热管制造与异种钢焊接等工艺,开展了填补国内基础研究空白的高温材料研制,研制出世界上体积最大的核反应堆压力容器、全球首台采用电磁轴承结构的大功率主氦风机、全球首台高温气冷堆螺旋管式直流蒸发器等堪称“大国重器”的核心设备,设备国产化率达93.4%( 远高于重大专项总体方案要求不低于75%的目标 ),为提升高温气冷堆产业基础能力和产业链现代化水平贡献了“华能经验”。本文以蒸汽发生器的研发、制造过程为例,讲述华能核电人和数万核电从业者的顽强拼搏、艰难创业之旅。
敢为人先,共克研发难题
蒸汽发生器设备是示范工程的核心主设备之一,其主要功能是将堆芯产生的热量由一回路传给二回路,产生蒸汽推动汽轮发电机组产生电能。蒸汽发生器总高约25米,最大外径约4.5米,总重约500吨,与主氦风机一起安装在蒸汽发生器壳体中,与反应堆压力容器形成肩并肩式布置,采用直流式螺旋盘管换热设备。该设计换热效率更高、结构布置更紧凑,在核电领域属创新型设计。蒸汽发生器也是示范工程设计和制造难度最大的核岛主设备。该设备由清华大学核能与新能源技术研究院设计,哈电集团( 秦皇岛 )重型机械有限公司生产制造。
因其设计复杂、制造难度大、无成熟经验借鉴,蒸汽发生器项目推进长期处于高温气冷堆示范工程建设的关键路径上。从2008年合同签订到2018年完成首台设备制造,历时10年,发布技术规格书、技术要求83份,涉及11万余个零部件,产生设计变更、设备材料变更等约800份。
在整个研发制造过程中,中国华能、清华大学、中核集团各级领导十分关注项目进展,定期举行高层会谈,决策重大技术问题。项目负责人常驻设备制造现场,发生问题时第一时间与清华大学沟通协调、寻计问策,联合设备厂家一道共谋解决之法,攻克了蒸汽发生器出口连接管布管及包裹的施工设计与优化、单根60米超长T22传热管研发和多头成型螺旋盘管工艺研发、T22管防锈工艺研究及工厂化制造、出口连接管模型件制造及布置工艺研发、出口连接管弯致裂纹失效分析与制造工艺优化、高精度换热单元套装工艺研发和工厂化制造、意大利Fomas出口蒸汽管板用800H大锻件入厂复验高温拉伸不合格安全评审、高温部件材料采购及长时高温持久与蠕变试验、高精度小口径换热管对接、镍基合金全位置TIG自动焊研究、大型内件与壳体最小处间隙不到1mm的精准套装、大型立式台架总装、大容积承压设备立式气压试验等共30余项世界性技术难题。十年磨砺,理想终成现实,图纸化身国之重器!
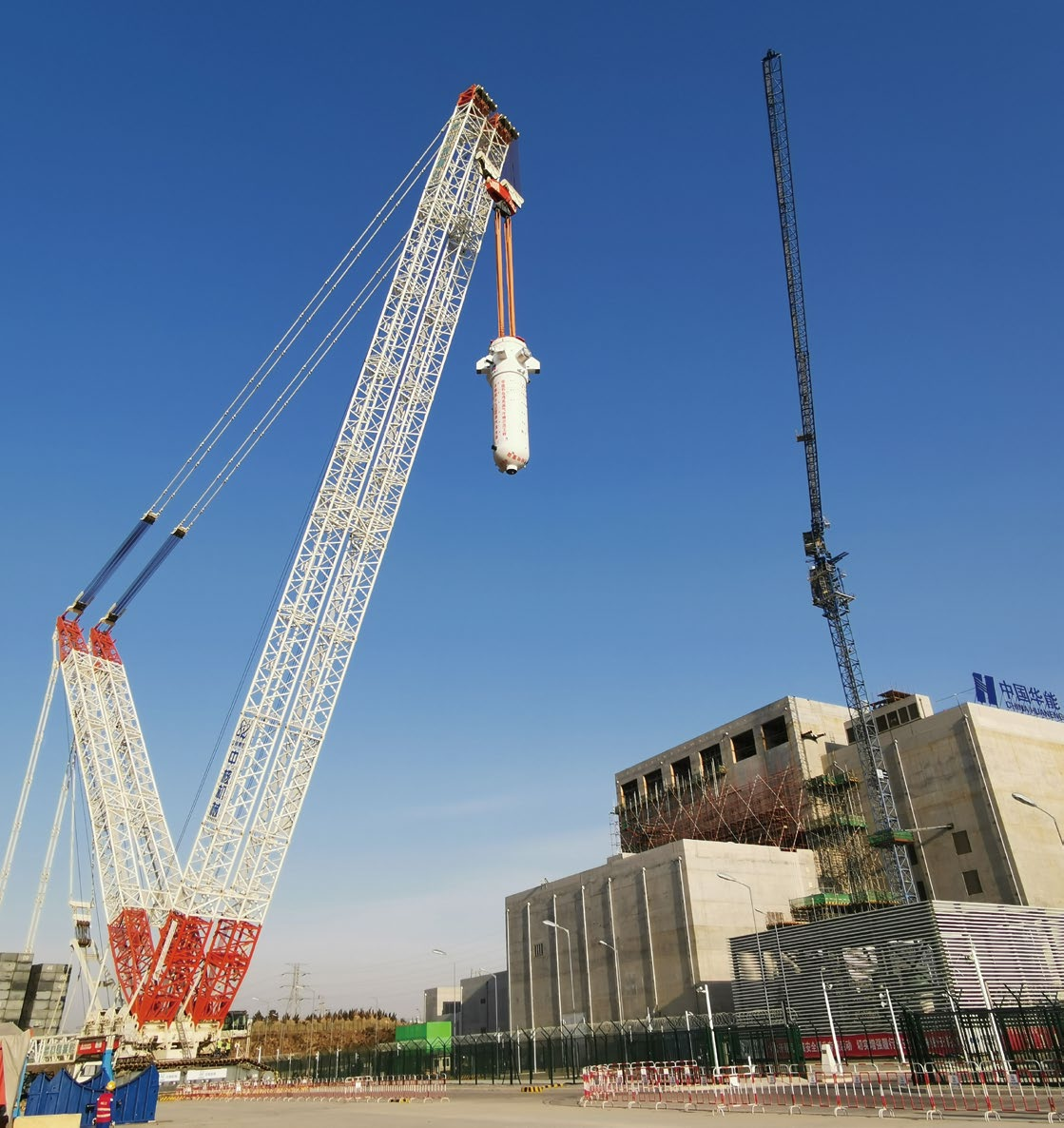
2019年1月27日,蒸汽发生器吊装
砥砺攻坚,攻克换热单元瓶颈问题
蒸汽发生器换热单元由中心筒、外筒、5层螺旋盘管、承重条和固定条等构成,对螺旋换热管成型尺寸、换热单元内外筒公差要求严格。承重条与换热单元各层螺旋盘管之间的间隙仅为0.5mm,总长8800mm,套装难度大,由江苏银环精密钢管有限公司承制。在清华大学核研院的技术支持下,江苏银环公司于2016年成功完成39个换热单元的套装与制造。
成功之路并非坦途。2017年初,蒸汽发生器核心部件——核安全1级出口连接管因为弯制裂纹而全部报废,设备制造主线工作完全停止。这对设备制造质量和工期的影响巨大,造成的损失远超预期。项目紧急且技术难度高,石岛湾核电副总经理张延旭与中核能源副总经理林立志迅速组建专项团队,选派精干力量入驻江苏银环,协调推进新传热管的生产进度及制造质量监督工作。驻厂人员深入研究传热管关键制造技术要求及相关改进工艺措施,不分昼夜在车间内巡检、与江苏银环技术骨干及操作人员对话、核实操作记录,掌握每根管材的准确生产进度及质量状态,提前预判各类问题隐患,及时协调处理渗透检验标准不统一、清洁度检查项目不完整等多项问题。主线生产工作24小时不停,项目团队在周末、中秋节、国庆节期间全程监督,连续驻厂7个月,出席监督见证点近200个,审查制造检验报告、记录近千份。最终1330根出口连接管全部按期发货,其弯制性能优良,成功打通了蒸汽发生器制造乃至高温堆示范工程的关键路径。石岛湾核电设计采购部王威作为专项团队的一员,全程入驻江苏银环,负责新传热管制造项目。他感慨道:“感觉这7个月做的事情意义重大。各方团结一心、目标高度统一,既打通了蒸汽发生器制造的关键路径,项目团队的管理能力和技术水平也得到了快速提升”。
精益求精,气压试验一次成功
新制造的出口连接管运抵哈电重装后,蒸发器主体制造关键路径重新启动。项目团队马上调整工作重心并入驻哈电重装,与制造厂工艺、焊接、质量检验及生产人员保持全面沟通,通过提前分析、判断设备制造风险点,对各关键工序全程监督管理。项目各方凝心聚力,以时不我待的干劲、咬定青山不放松的韧劲、不破楼兰终不还的冲劲,最终攻克了狭小空间传热管对接焊、内件与壳体套装、镍基合金全位置TIG自动焊等一系列制造难点。
业内蒸汽发生器通常采用水压试验验证承压焊缝强度,但高温气冷堆蒸汽发生器由于其结构特殊性,只能采用气压试验进行验证。该气压试验较水压试验难度更大、失败风险也更大。石岛湾核电、中核能源、清华大学及制造单位高度重视,建立了从公司高层到项目经理层的项目团队,形成高效的管理协调机制。项目团队全程驻厂、精心策划,讨论制订试验规程并不断完善,及时决策采用专用立式总装台架,并配置专用气压试验设备,全面落实人员、工器具、备件保障工作,为蒸汽发生器气压试验一次成功打下了坚实基础。
2018年9月29日23时58分,高温气冷堆示范工程首台蒸汽发生器在哈电重装顺利完成壳程和管程气压试验,并取得一次性成功,开创了国内核电行业核岛主设备制造密封性检验的先河,标志着蒸汽发生器设备最后一个关键制造难点被攻克,高温气冷堆示范工程设备研制领域取得了突破性进展。高温气冷堆重大专项总设计师、清华大学核研院院长张作义回忆说:“那天晚上时刻都关注着蒸汽发生器气压试验进展状态,每到一个保压台阶都会打电话了解情况。直到凌晨试验成功那一刻,心里终于才踏实了,蒸汽发生器最后一个关键制造难点被攻克了!”
2019年1月,高温气冷堆示范工程核岛主设备中历时最长、制造难度最大的蒸汽发生器首台到货,激动的泪水在项目团队脸上流淌:“我们终于成功了!”

党建引领,完成节流组件安装
节流组件是调节蒸汽发生器设备正常运行的“钥匙”。蒸发器主体设备到货后,节流组件的安装进度成为制约冷试工作的关键所在。
在石岛湾核电“党建引领 聚力攻坚”党员示范行动的感召下,石岛湾核电、中核能源、清华大学、制造厂组建“节流组件到货及安装”攻坚团队,形成了干事创业的强大合力。攻坚团队提前组织安装单位开展节流组件模拟装配试验、防松组件焊接工艺试验等验证性工作,提前识别出防松板安装间隙不足、防松组件焊接变形过大等多个重大风险点,针对性制定安装工艺措施并列入现场操作规程,提前进行防松板试装及装配加工,研发焊接保护工装、专项磨练焊工技能。现场安装工作准备充分细致,实现了节流组件到货验收、安装、焊接各环节无缝衔接。通过优化人员排班,日夜奋战2个月,最终保质保量完成了节流组件安装工作,为蒸汽发生器后期顺利运行奠定了基础。
蒸汽发生器的研制成功只是高温气冷堆示范工程攻坚路上的一个小缩影。在国家科技重大专项领导小组的领导下,中国华能坚决扛起责任使命,与清华大学、中核集团、科研院所等单位组建联合体,攻克了一系列世界性设备研制关键技术难题,形成了一整套重大专项科技创新实施机制与管理经验,培养出众多具有专业技术能力的核电创新人才,以强烈的责任担当铸就了“大国重器”。
(作者系华能山东石岛湾核电有限公司 王威 席京彬 吴志军 侯雪梅)
免责声明:本网转载自合作媒体、机构或其他网站的信息,登载此文出于传递更多信息之目的,并不意味着赞同其观点或证实其内容的真实性。本网所有信息仅供参考,不做交易和服务的根据。本网内容如有侵权或其它问题请及时告之,本网将及时修改或删除。凡以任何方式登录本网站或直接、间接使用本网站资料者,视为自愿接受本网站声明的约束。