核工业产品具有结构复杂、性能要求苛刻、作业环境恶劣、牵扯学科多等特点。目前设计单位已经普遍采用了多种CAD工具进行产品研发,但在设计过程一直缺乏良好的协同及虚拟验证手段。随着用户方对产品质量、交付周期等的要求越来越严格,必须打破设计、制造、施工、维修维护等部门间的技术隔离现象,加强各单位的协同能力,实时交互,并行开展工作,才能更好的在设计过程中尽早的发现在后续工艺、生产制造、施工、维修维护等环节中可能存在的问题,减少错误,避免大规模的返工。
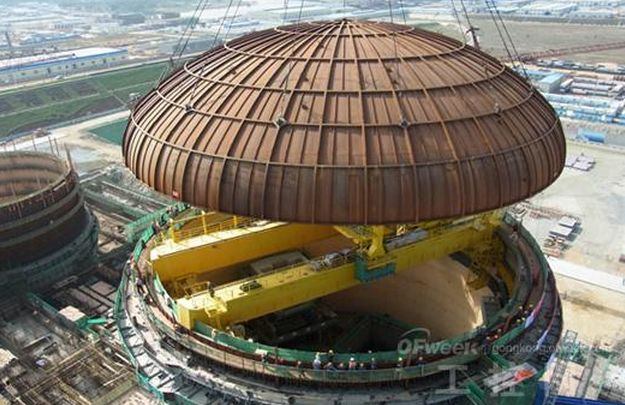
IC.IDO虚拟现实解决方案
ESI集团IC.IDO可视化虚拟决策平台在核工业领域主要用于虚拟工程(核电站布局、异地协商、柔性布线等)、虚拟评审、虚拟装配、虚拟维护、人机工效、培训等,为核工业产品的设计、实施、维护等提供强有力的解决方案。
1.大数据量异构模型支持
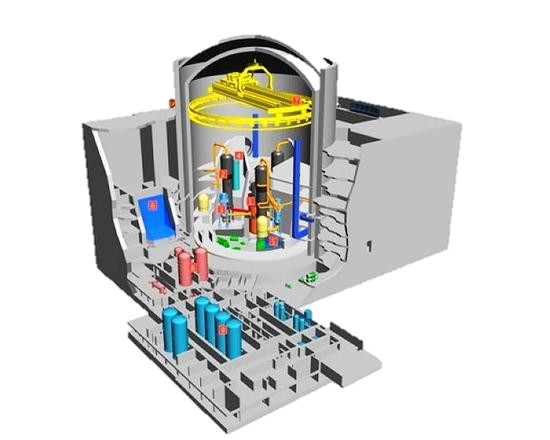
在核工业产品的设计中分别使用CATIA、SolidWorks、Plant 3D等多类不同的CAD软件进行土建、结构、机械、电气、管路等不同部分的设计,相关的产品模型尺寸大、零部件多、来源复杂,评审过程需要将不同CAD的设计结果导入到一个环境中,在一个软件平台中组装起来进行设计验证。传统的CAD环境中只能实现局部模型的展示,无法实现完整的总装模型展示,很难实现多专业的可视化综合协调及决策。因此急需一个能够支撑超大模型、展示评估的软件环境,以支持在研发过程中的多专业协调、评审等方面的应用。
利用IC.IDO的大数据处理引擎,解决了传统CAD软件难以支撑核工业领域大数据量模型运行的问题,可同时将多种设计模型快速导入到平台中,在1:1的虚拟现实环境中,多方人员可以快速理解设计意图、发现设计缺陷,进行设计验证、多方案比选等仿真工作。
2.可施工性、可装配性的设计验证
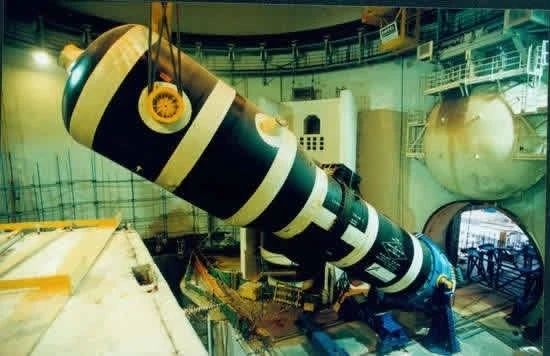
对于可施工性、可装配性的设计验证,目前大多需要依靠设计师的经验判断,或在后期的建造中,发现问题现场处理。这种因前期设计缺陷带来的设计变更导致项目延期严重,因此需要引入可施工性、可装配性的设计验证工具,以实现在设计过程中能够提前进行虚拟仿真验证,提前发现问题,减少现场问题的产生。
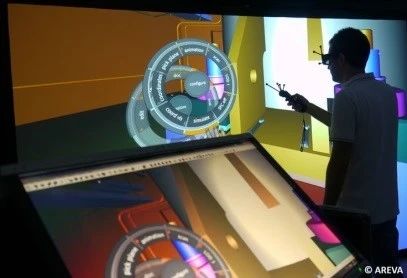
在设计阶段,就可利用IC.IDO虚拟仿真技术,并结合现场待装配组件、吊装设备、现场环境等来进行可施工性、可装配性的仿真验证,制定施工序列、大部件装配路径等工艺规程,减少设计错误带入后期施工,变“后现场实施”为“先虚拟验证”,大量节省研制经费、缩短研制周期。
3.维修维护性验证
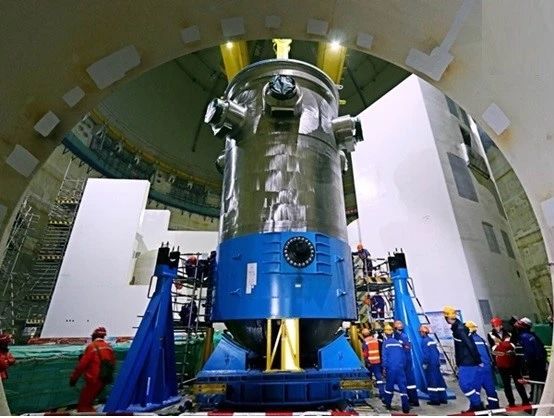
目前维修维护性设计工作一般在设计基本完成后才能开始,且主要依赖于经验和实物样机试验,在整个产品设计环节中相对滞后。为了减少工程变更、缩短工程项目建设周期、便于工程产品的后续维修维护,需要在设计过程中,提前开展维修维护性的虚拟仿真验证工作。
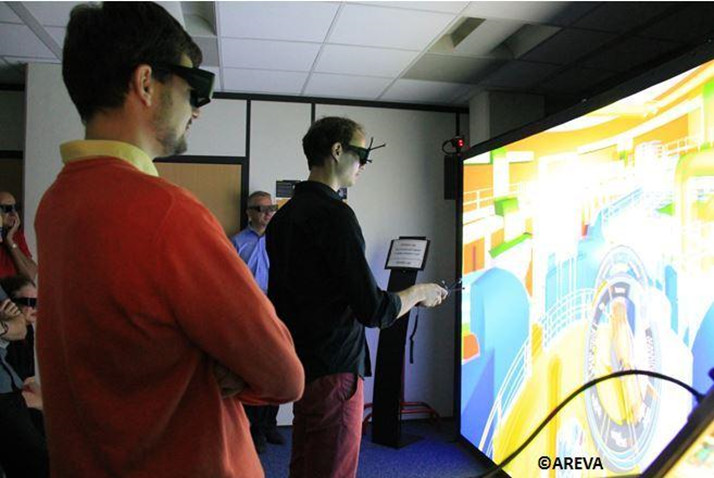
在设计阶段利用IC.IDO平台进行维修维护性验证,结合工装、工具进行维修过程仿真、预估产品的维修维护性能,并形成准确的维修维护规程,用于指导、培训维修维护人员,大幅缩短了产品维护周期,降低维护成本,保证核工业产品正常高效的运行。
免责声明:本网转载自合作媒体、机构或其他网站的信息,登载此文出于传递更多信息之目的,并不意味着赞同其观点或证实其内容的真实性。本网所有信息仅供参考,不做交易和服务的根据。本网内容如有侵权或其它问题请及时告之,本网将及时修改或删除。凡以任何方式登录本网站或直接、间接使用本网站资料者,视为自愿接受本网站声明的约束。